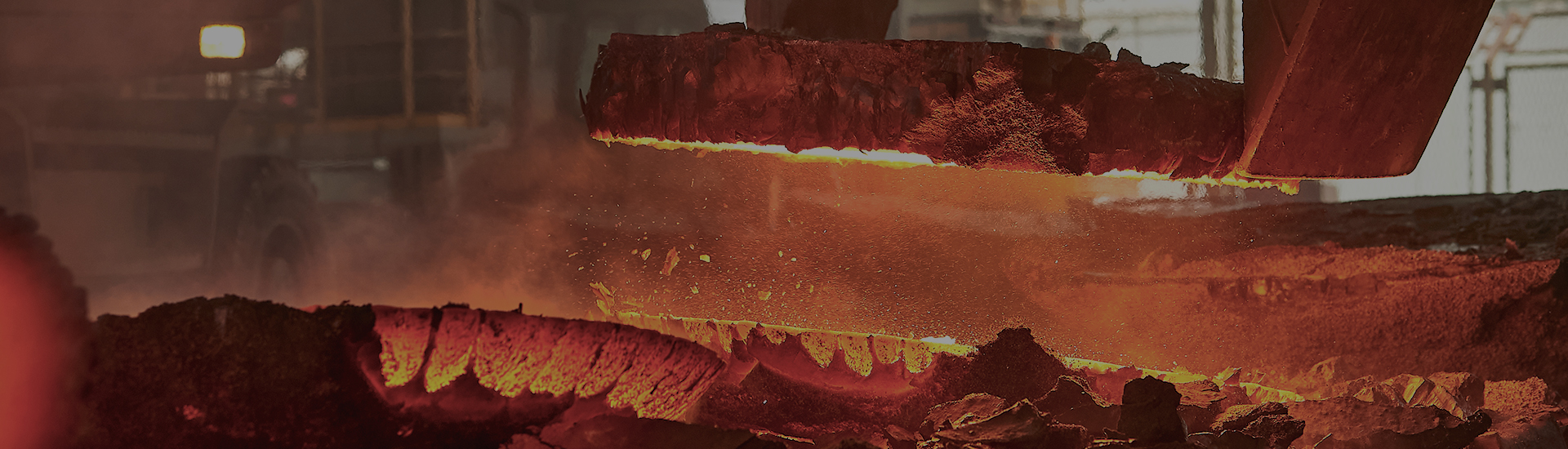
Process and Technology
We have molybdenum concentrate roasting facilities equipped with an integrated production system, and we produce molybdenum-processed products that were previously exclusively imported.
LEACHING
Leaching Process
Molybdenite (MoS2)
Copper Cement (Cu Powder)
Copper(Powder, by-products)
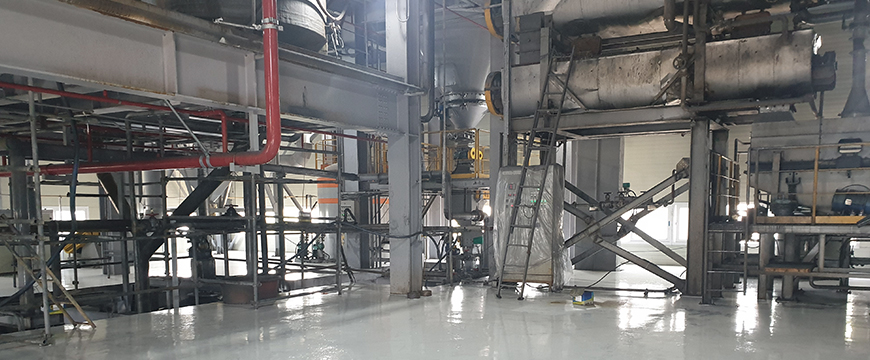
Operate hydrochloric acid leaching facilities for molybdenum concentrates
We produce L-Cu molybdenum concentrates by selectively removing the copper components from H-Cu concentrates using hydrochloric acid.
Selective recovery of copper components from solutions leached with hydrochloric acid
We implement ESG management by transforming copper from hydrochloric acid wastewater into a resource.
Main Features
-
01
We remove copper components selectively from MoS2 using hydrochloric acid.
-
02
MoS2's residual hydrochloric acid and moisture are consistently removed by disc filters after the leaching process.
-
03
By recovering copper components that are heavy metals leached in hydrochloric acid, we create added value and contribute to Seah M&S's ESG management.
MoS2 ROASTING
Roasting Process
Molybdenum oxide powder
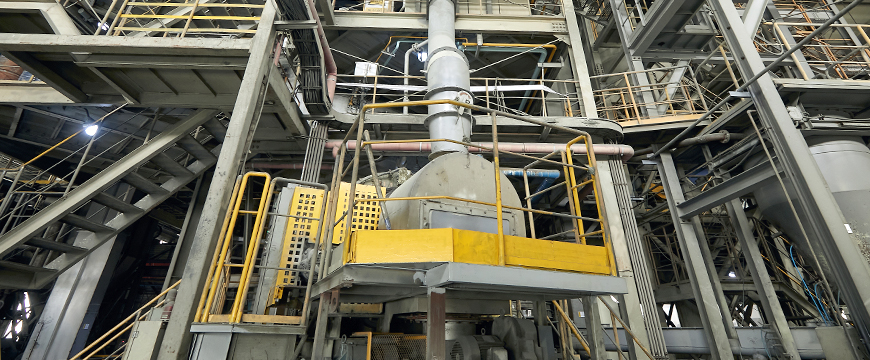
Multistage Roaster Facility
Through our roasting technology mastered after many years of effort, we can produce molybdenum products and are equipped with cutting-edge desulfurization facilities and wastewater treatment facilities.
Resource Recovery of Desulfurized Waste Gas
Seah M&S implements EGS management by capturing and utilizing rare materials in the sulfur dioxide gas produced by the multistage roaster and recovering resources from the desulfurization chemical.
Main Features
-
01
The stable temperature control of the multistage roaster at each stage ensures consistent molybdenum oxide quality.
-
02
We produce products to meet customer demand and have a capacity of the greatest production in Korea.
-
03
The electric precipitator (EP), sulfur dioxide gas desulfurization facility, rare metal-capturing facility, and deodorization facility are maintained in the finest possible condition.
FERRO MOLYBDENUM
FeMO Production Process
Ferro Molybdenum (FeMo)
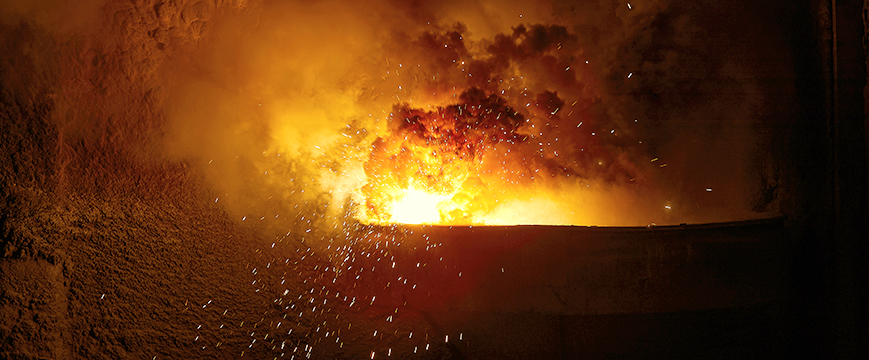
Producing Molybdenum, a Key Ingredient in Stainless and Specialty Steels in Steel Industries Across the Globe
Our ferromolybdenum production process converts molybdenum oxide into a metallic form by implementing silicon and aluminum reduction reactions.
Batch Thermite Reactions
Easy-to-transport vats are used to ensure the rapid mass production of our FeMo products.
Main feature
-
01
Using our cutting-edge automated measurement systems to combine a precise ratio of primary and secondary materials, we can ensure that our molybdenum products are fine-tuned to our client's exact needs and specifications.
-
02
All secondary materials used in thermite reactions come from recycled sources, and all byproducts produced by the molybdenum production process are also recycled as resources, ensuring that we are fully compliant with RE100 efforts.
-
03
The FeMo lumps produced by the thermite reaction are sent through a jaw crusher and a sorting machine to ensure that the products we provide to our clients are of a uniform size.